桌面數控車床結構的優化設計
2017-6-29 來源: 四川大學制造科學與工程學院 作者:黃紀剛 方輝 蔣滔 董秀麗
摘要:針對微小零件的加工制造,設計了1臺桌面級數控車床。用Solidworks軟件進行車床的結構設計,重點使用Solidworks軟件中的 Simulation Xpress模塊對車床關鍵部件的結構進行有限元靜力學分析,經過計算求解,模擬出各部件在實際工作時所受的應力以及應變分布情況。根據計算結果,對結構進行針對性地優化。在優化的過程中,主要以質量最小化為優化目標,使結構在滿足力學性能的前提下,盡可能輕量化,以降低成本。最終根據優化后的設計方案構建出桌面級車床。
關鍵詞:車床;Solidworks;優化設計;有限元分析
隨著社會的發展,人們趨于追求許多常用產品的小型化和微型化,制造業將面臨越來越多加工微小零件的情況[1]。目前,數控機床作為制造業主要的制造設備,具有效率高、加工能力強等優點,但對于一些價值較低的微小零件來說,常規尺度的數控機床的加工成本較高。針對這樣的需求,設計了1臺桌面級數控車床,并采用有限元分析方法對初始設計方案進行了優化。桌面級機床的發展是對制造技術和制造裝備的有益補充[2],它具有體積小、成本低、結構簡單、傳動效率高等特點,具有廣泛的適用性。
1.車床結構設計
機械結構設計的傳統方法需要大量的手工繪圖,并根據設計者的經驗來確定機械零件的結構。這種方法不僅勞動量大,而且無法科學地考察機械件結構設計的合理性,從而難以在設計初期及時發現設計的不當之處,導致出錯率高,容易造成經濟上的浪費。隨著 CAD 軟件的出現和流行,機械結構設計的傳統方法逐漸被摒棄,利用功能強大的 CAD 件幫助設計人員完成機械結構的設計成為了現代機械設計的主流方法。利用現代 CAD 軟件設計機械結構不僅能有效地避免勞動量大、出錯率高、缺乏力學驗證等不足,同時也縮短了設計周期、降低了設計成本[3]。Solidworks軟件是目前行業內主流的 CAD軟件之一,其功能強大,集三維建模、工程圖制作、虛擬裝配、運動仿真、有限元分析優化等功能于一體,完全能夠滿足現代機械設計的全部要求[4]。
本文采用Solidworks軟件設計了桌面型車床的結構,設計流程框圖如圖1所示。

圖1 桌面型車床的結構設計流程框圖
設計的桌面級數控車床的裝配體如圖 2 所示。其主要技術參數如下:
1)床身尺寸為580mm×260mm×180mm,中心高為40mm;X、Y 方向行程分別為280 、150mm;選用自定心三爪卡盤,其夾持直徑為2~22mm;
2)X、Y 方向分別由1對線性導軌實現其進給運動的導向。設計中選用 THK 超小化設計的 RSR系列導軌,其行走平行度精度可達 0.017 mm。X軸導軌選型為2RSR5N300L,Y 軸導軌選型為2RSR3N160L;選用精密滾珠絲杠作為車床傳動件,X 軸絲杠選型為 BNK1202,Y 軸絲杠選型為 BNK1002。
3)主軸傳動采取傳動比為 1∶1.4的同步帶一級傳動,減少了許多中間傳動機構,降低了傳動的誤差,提高傳動效率;同時,主軸箱的結構簡單,整體尺寸較小,符合該桌面型數控機床的設計理念[5]。
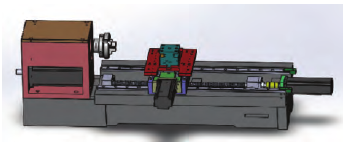
圖2 桌面級數控車床裝配體的設計原理圖
2.基于Solidworks軟件的結構分析
Solidworks軟件具備優秀的有限元分析能力。可供設計者在制作工程圖進入實際加工之前,對所設計的零部件結構進行科學地分析并優化求解,以達到結構最優。采用Solidworks軟件進行結構有限元分析的一般流程為前處理、分析計算以及后處理[6]。前處理包括建立有限元模型、添加夾具、添加載荷以及指定材料;分析計算是軟件根據設置自動進行網格劃分以及計算求解;后處理則包括計算結果的顯示與分析,檢查其正確性,并可生成分析報表[7]。通過有限元對結構進行分析后,采用 Solid-works軟件進一步對結構進行優化。現以床身為例,說明利用該軟件對結構進行分析及優化的過程。
床身是機床的基礎,本次設計 采用的是 臥式床身結構,并在床身下方布置排屑孔及排屑槽。床身采用優質鑄鐵整體鑄造而成,并合理布置筋板,使床身在具有良好剛性的同時,用料最少,節約成本。另外,設計的床身上的所有加工表面均位于鑄造面上部,使之后的加工更加簡單;主軸箱安裝面與 X 方向導軌安裝面的基準一致,能有效保證主軸中心與 X軸平行。床身的前處理過程如圖3所示。
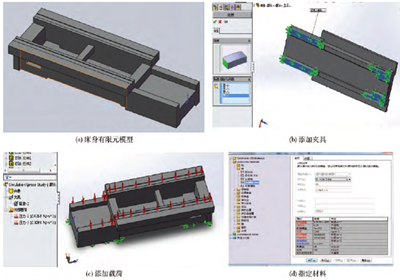
圖3 床身前處理過程
1)床身結構的有限元建模圖3(a)為桌面型車床床身的有限元模型。 建立其床身有限元模型時,忽略了各處的過渡圓角以及床身上的所有螺栓孔,因為這些結構不會對床身整體的質量及力學性能產生大的影響 ,忽略這些結構能簡化模型,提高計算速度[8]。 模型建立完成后,選擇Simulation Xpress插件為床身定義算例。
2)添加夾具添加夾具即為分析對象添加固定約束。設計的車床通過床身底部的 4個平面支撐,指定床身的固定約束,如圖3(b)所示。
3)添加載荷床身主要受到主軸箱以及進給機構的正壓力,通過Solidworks中質量屬性估算出主軸箱自重約為178N,進給機構自重約為163N。分別為主軸箱支撐面和導軌安裝面添加正壓力為14.350、13.008kPa,如圖3(c)所示。
4)指定材料指定床身材料為灰鑄鐵,灰鑄鐵的泊松比為0.27,拉伸強度為151 MN/m2,抗壓強度為572MN/m2,如圖3(d)所示。
5)分析與計算根據設置的參數,采用 Solidworks對床身結構進行有限元分析計算,模擬床身在工作狀態下所受的應力及其變形情況,如圖4所示。由結果分析可知:床身所受最大應力出現在床身中部,約為46.209 18kPa;最大應變出現在床身中部兩側,變形量約為2.2×10-4mm。
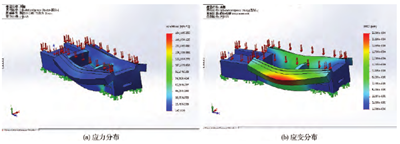
圖4 分析結果
3.結構優化
由計算結果可知,床身受到的最大應力遠 小于其拉伸強度,且變形很小,其結構還可進一步優化。由床身結構有限元分析的應力分布和應變分布能夠看出,床身主軸箱安裝部位的應力和應變都最小,故可作為結構優化的重點部位。在有限元分析的基礎上,采用 Solidworks軟件對結構進行優化,需要指定優化的變量、給定約束條件以及確定優化的目標。本文主要針對桌面級車床的輕量化設計,故指定床身主軸箱安裝部位的厚度為變量,以安全系數為約束條件,優化求解的目標為質量最小化。床身結構優化設置和結果如圖5所示。指定變量的初始尺寸為20mm,同時人為設置變量的上、下限分別為35和10mm,設置的最小安全系數為2.3。采用Solidworks進行優化求解,優化后變量尺寸為27mm,即主軸箱安裝部位的厚度減少了7mm。床身初始質量約為32.862kg,優化后質量約為30.674kg。通過比較可知,優化后的床身結構更加合理,降低了成本。
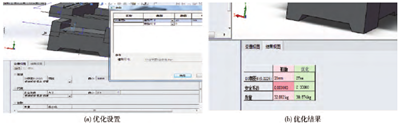
圖5 床身結構優化設置和結果
通過對關鍵部件結構的有限元靜力學分析以及結構優化,使設計方案更為合理,最終完成了桌面級車床的設計,并構建了其實體,如圖6所示。
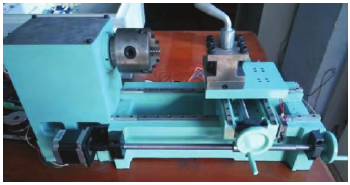
圖6 桌面級車床實體
4.結論
1)采用 Solidworks軟件進行機械結構設計,便于設計者查看、校對、修改以及表達設計方案,能極大提高設計效率。
2)采用Solidworks軟件對結構進行有限元靜力學分析,計算出各部件在工作狀態下的應力和應變分布情況,供設計者考察結構設計的合理性,同時也為結構優化指明了方向。
3)Solidworks軟件 在結構優 化 中 的 應 用,能 幫助設計者科學地優化其設計方案,以追求結構設計的最優化。
投稿箱:
如果您有機床行業、企業相關新聞稿件發表,或進行資訊合作,歡迎聯系本網編輯部, 郵箱:skjcsc@vip.sina.com
如果您有機床行業、企業相關新聞稿件發表,或進行資訊合作,歡迎聯系本網編輯部, 郵箱:skjcsc@vip.sina.com