利用普通車床加工細長桿零件的工藝改進
2017-11-15 來源: 包頭職業技術學院車輛系 作者:賈玉梅
摘 要:通過改進細長桿零件裝夾方法、跟刀架的結構及調整方法,優化刀具的幾何參數,改變刀具的安裝位置和車削走刀方向后,加工完成的細長桿零件尺寸精度、形狀精度等加工精度滿足圖樣要求,省去了成品校直工序,降低了加工成本,縮短了加工周期,提高了生產效率。
關鍵詞:零件;刀架;刀具;加工精度
所謂細長桿是指零件的長度L 與直徑d 之比≥25。與一般的軸類零件相比,細長桿零件存在工件細長、剛度差及受熱影響變形較大的特點,這給車削加工帶來很大的困難,不容易獲得良好的幾何精度[1-2]。在普通車床上的常規車削方法是:先將細長桿零件裝夾于車床主軸箱的三爪自定心卡盤和尾座的頂尖之間,然后在中心架、跟刀架的配合下,采用正向切削法用標準刀具進行車削。由于細長桿零件本身結構的特點以及加工工藝的原因,車削完成的細長桿零件有較大的彎曲變形[3-4]。為了使零件達到圖樣要求的精度,應增加校直工序,零件精度要求越高,校直的次數越多。盡管經過了校直工序,有些細長桿零件還是因為不能滿足圖樣要求而報廢。
1 、改進加工工藝技術方案
加工工藝改進方案如下;
1)細長桿零件夾緊措施。用卡爪定心、夾緊細長桿零件時,在3個卡爪與零件的接觸面之間分別墊1個4~6mm的鋼絲段,細長桿零件裝入卡爪的長度為15~20mm,鋼絲段橫向放入卡爪的防滑槽內,
2)跟刀架的結構形式及調整順序。跟刀架采用3個支承爪結構,調整順序依次為:后支承爪→上支承爪→下支承爪。
3)車刀安裝位置。粗車時,刀尖應高于細長桿零件軸向中心線0.4~0.6mm;精車時,刀尖應低于細長桿零件軸向中心線0.1~0.2mm。
4)走刀方向。走刀方向為反向切削。
5)尾座頂尖預緊力的調整。車刀參與切削前,尾座頂尖預緊力的調整方法如下:用手捏住轉動的尾座頂尖,尾座頂尖即停止轉動,而細長桿零件仍然轉動;松手后,尾座頂尖能隨著細長桿零件繼續同步旋轉,尾座頂尖的頂緊力達到這種狀態時開始進行切削工序。
6)車刀幾何參數。主偏角75°~80°、前角20°~30°、刃傾角3°~5°、主后角10°~15°、副后角2°~3°,前刀面磨R1.5~R3mm 的斷屑槽,刀尖圓弧半徑<0.3mm。
7)熱處理。粗加工后熱處理:中溫時效溫度400℃,保溫4h,隨爐冷卻;彎曲度若不滿足要求,需要增加校直工序,之后低溫時效溫度200~240℃,保溫2~3h,隨爐冷卻。
2、改進加工工藝與常規加工工藝對比
2.1 裝夾方法
常規的裝夾方法,三爪和頂尖將細長桿零件剛性夾緊,所以在車削過程中,細長桿零件由于切削力、切削熱及自重的影響而產生的變形無法調整,切削過程中這種變形的不斷積累,必然導致細長桿零件產生嚴重的彎曲變形。改進的裝夾方法,用卡爪定心、夾緊細長桿零件時,在3個卡爪與細長桿零件的接觸面之間分別墊1個5mm 的鋼絲段。細長桿零件裝入卡爪的長度為15~20mm,鋼絲段橫向放入卡爪的防滑槽內,由于鋼絲段為柔性結構,所以當細長桿零件在切削狀態產生熱變形時,可以起到方向調節的作用,或在細長桿零件靠近卡爪處車一段“縮頸”,也可以實現方向調節的目的。這些措施的實施,可以有效控制細長桿零件在車削過程中的變形,從而減小或避免細長桿零件的彎曲變形。
2.2 車削的走刀方向
常規的走刀方向為正向切削,即從尾座向主軸箱方向的切削,切削產生的軸向分力指向主軸箱,由于細長桿零件剛性裝夾于三爪自定心卡盤上,無法消除切削產生的軸向分力,這就使細長桿零件受壓而產生彎曲變形。
改進的走刀方向為反向切削,即從主軸箱向尾座方向的切削,切削產生的軸向分力指向尾座,此時如果尾座頂尖的頂緊力合適,將會平衡掉這個軸向分力,從而使細長桿零件受熱伸長后的變形量得以釋放,從而避免細長桿零件的彎曲變形。
2.3 尾座頂尖預緊力的調整
車刀參與切削前,用手捏住旋轉的尾座頂尖,尾座頂尖即停止旋轉,而細長桿零件仍然旋轉;松手后,尾座頂尖能隨著細長桿零件繼續同步旋轉,尾座頂尖的預緊力達到這種狀態時,就可以使細長桿零件受熱伸長后的變形量隨著尾座頂尖預緊力的變化而釋放。
2.4 跟刀架的安裝
2.4.1 跟刀架的結構
常規的跟刀架結構為2個支承爪結構,上面1個,后面1個。細長桿零件由于沒有對稱的平衡力夾緊,所以在車削過程中,由于本身的重力及不可避免的彎曲,會因離心力瞬時離開或接觸支承爪而產生振動,從而不能保證細長桿零件加工的尺寸精度和形狀精度。
改進的跟刀架結構為3個支承爪結構:上支承爪、下支承爪和后支承爪。跟刀架的3個支承爪與車刀組成2對平衡的徑向力,使細長桿零件在車削時,上下、前后都不能移動,車削過程穩定,不易產生振動,從而保證了細長桿零件加工的尺寸精度、形狀精度和表面粗糙度要求。
2.4.2 支承爪的調整順序
跟刀架支承爪的調整,先調整后支承爪,即與車刀相對的支承爪,以確保刀具的切削位置,再順序調整上支承爪和下支承爪,保證工件重力方向支承和夾緊的平衡性。調整時,綜合運用手感、耳聽和目測等方法,使跟刀架的支承爪剛好接觸細長桿零件。如果跟刀架的支承爪和細長桿零件接觸壓力過大,會把細長桿零件車成竹節形,反之則不能起到跟刀架的作用。
2.4.3 基準外圓的車削
裝夾細長桿零件后,在靠近三爪自定心卡盤處車長度約40mm的基準外圓,用于安裝跟刀架。切削量大小視細長桿零件毛坯料的實際情況而定。
2.5 車刀的幾何參數
常規車刀的幾何參數為:前角10°~15°、主偏角80°~93°、刃傾角0°、主后角6°~8°。改進車刀的幾何參數如下:1)為減小細長桿零件彎曲變形,車削過程中徑向切削力越小越好,合理的車刀主偏角為75°~80°;2)為減小切削力和切削熱,應選擇較大的車刀前角20°~30°;3)車刀前刀面磨R1.5~R3mm的斷屑槽,使切削順利卷曲折斷;4)車刀刃傾角選擇3°~5°,使切屑流向至待加工表面;5)車刀切削刃表面粗糙度>Ra0.4μm,并要經常保持鋒利;6)為降低車刀的磨損,選較大的主后角10°~15°,另外在車刀主后角的最前端即從刀尖開始磨出副后角2°~3°,副后角可起到支承工件,有效減小徑向切削力,使加工平穩的作用,刀尖圓弧半徑<0.3mm。
2.6 車刀的安裝位置
在常規車削時,刀具的刀尖與細長桿零件的軸向中心線齊平,很容易出現扎刀現象。
改進的裝刀位置:粗車工序,裝刀時刀尖應高于細長桿零件軸向中心線0.5mm,可避免產生扎刀現象;精車工序,裝刀時刀尖應低于細長桿零件軸向中心線0.1mm,可起到支承零件的作用,使車削過程更加平穩、可靠,車削效果更好。
2.7 車刀材料及規格
粗車工序選用耐磨性好的硬質合金車刀(YT15、YT30)。精車工序選用高速鋼寬刃車刀(W18Cr4V寬刃車刀),可進行大走刀量切削,從而提高細長桿零件的尺寸精度,降低表面粗糙度。刀具材料與常規車削選用的相同,但精加工時選用的刀具規格不同,即寬刃車刀。
3 、裝夾結構示意圖
裝夾結構示意圖如圖1所示,局部放大示意圖如圖2所示。
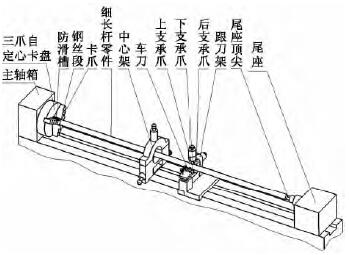
圖1 裝夾結構示意圖
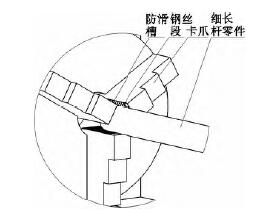
圖2 裝夾結構局部放大示意圖
4、結語
通過改進細長桿零件裝夾方法,改變車削的走刀方向和刀具的安裝位置,改進跟刀架的結構及調整方法,優化刀具的幾何參數,加工完成的細長桿零件尺寸精度、形狀精度等加工精度滿足圖樣要求,省去了成品校直的工序,降低了加工成本,縮短了加工周期,提高了生產效率。
投稿箱:
如果您有機床行業、企業相關新聞稿件發表,或進行資訊合作,歡迎聯系本網編輯部, 郵箱:skjcsc@vip.sina.com
如果您有機床行業、企業相關新聞稿件發表,或進行資訊合作,歡迎聯系本網編輯部, 郵箱:skjcsc@vip.sina.com