數控車床梯形螺紋的加工方法及改進研究
2021-10-14 來源:常州科技經貿技工學校 作者:陳 靜
摘要:本文以梯形螺紋 Tr36×6 的加工工藝作為研究對象,針對梯形螺紋的結構參數與直進法、斜進法、左右切削法、直槽法、階梯槽法、分層切削法等加工方法進行詳細分析,并以常規加工方法存在的刀具磨損、排屑困難、生產效率低等工藝缺陷作為切入點,探討了實現高轉速粗車加工與低轉速精車加工兩道工序間良好銜接的具體方法及程序設計思路。經多次調試與驗證后發現,以每分鐘 560r 的轉速進行粗車加工,再將轉速下調至每分鐘 25r 進行精車加工,即可實現對梯形螺紋的變速加工,且保障梯形螺紋工件的質量達標,有效提高生產環節的效率,為梯形螺紋副的批量化生產創設有利條件。
關鍵詞:數控車床;梯形螺紋;變速車削
梯形螺紋主要應用于傳動機構中作為傳導螺紋,梯形外螺紋與內螺紋以成對方式呈現,具有牙型深、螺距較大等特征,在采用數控車床進行加工時易產生較大的切削力與振動問題,加劇刀尖磨損程度、易引發扎刀事故,影響到工件的質量與加工生產進度。基于此,本文擬針對梯形螺紋的常規加工工藝進行改進,并通過程序調試確保工藝具備可行性。
1、 梯形螺紋結構與加工方法
1.1 梯形螺紋。
1.1.1 基本結構。
選取一對典型梯形螺紋副作為參照,在該梯形螺紋副的左上方、右上方分別設有螺桿和螺套,兩類零件的外形、尺寸與螺紋精度將直接決定零件能否正常旋合。以梯形螺紋 Tr36×6 為例(各結構的參數如表 1 所示),其牙型呈等腰梯形、牙型角為 30°,相較于其他螺紋在牙根強度、對中性上占據良好性能優勢,其公稱直徑為 36mm、螺距為6mm。左旋螺紋需在尺寸規格后加注“LH”,右旋螺紋則不標出。為保障梯形螺紋質量達標,應在加工環節確保牙型的準確度,使螺紋中徑與基準軸保持同軸,以中徑尺寸定心,在車削加工環節注意控制好中徑的尺寸公差與兩側表面粗糙度[1]。
表 1 梯形螺紋的結構及計算公式
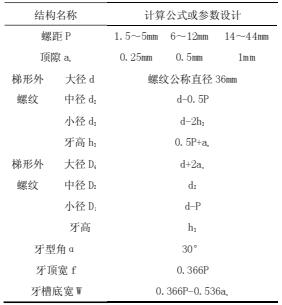
1.1.2 車刀材料。
在車刀材料選取上,主要選用硬質合金刀片進行梯形螺紋的高速車削,考慮到數控車床存在較嚴格的加工標準,因此選用材質為 YT15 硬質合金的可轉位機夾刀片,保障刀片在硬度、耐磨性與使用壽命等方面具備良好的性能優勢。
在車削加工環節,應注重選用標準刀片,在安裝刀具時控制主切削刃與工件軸線保持等高且平行,利用樣板進行找正與糾偏處理,使刀頭角平分線與工件軸線呈垂直關系,并且將車削深度控制在與牙型高度一致的位置,確保中徑尺寸達標。
1.2 加工方法。
1.2.1 直進法和斜進法。
直進法指車刀沿水平方向間歇進給至牙深部位,考慮到在車削梯形螺紋需利用車刀三刃同時切削,由此將產生較大的切削力、加劇刀具的磨損情況,并且無法保障及時排屑,易出現扎刀問題。斜進法指以牙型角方向為基準,將車刀沿斜向間歇進給,能夠有效減少切削力及產生的排屑量,但針對螺距較大的梯形螺紋進行加工時,仍面臨刀具磨損與牙型角存在偏差等問題,缺乏良好適用價值。
1.2.2左右切削法。
該方法指以牙型角反向為基準,將車刀錯位進給、實行單刃切削,借此有效規避多刃切削引發的扎刀問題,既有助于提升螺紋的車削精度,同時也可優化梯形螺紋表面質量,但也存在編程復雜的問題,無法保障加工效率。1.2.3 直槽法和階梯槽法。采用直槽法進行螺紋加工,應確保切槽刀的刀頭寬度不超過牙槽底寬,以小徑為參考沿橫向直進切至指定的直槽深度,并且留足 0.2mm 余量,隨后改用梯形螺紋刀沿斜向進行加工。
該方法將數控編程進行簡化,但同樣不適用于大螺距的螺紋加工,影響到排屑效果,加之刀頭較長影響到梯形螺紋刀的強度,極易在加工過程中產生刀頭折斷的問題。采用階梯槽法進行加工時,通常需先完成牙槽的分層,控制切槽刀沿左右方向移動切削出階梯槽,再改用梯形螺紋刀沿斜向進行加工。該方法具有良好的排屑效果,可實現梯形螺紋的批量化加工,但在將切槽刀更換為梯形螺紋刀時無法保障刀體對準螺旋直槽,易引發倒牙問題。1.2.4 分層切削法。該方法主要將直進法與左右切削法進行整合,先利用切槽刀將牙槽劃分為多個梯形槽,再依照直進、左右移動的順序進行各層梯形槽的車削加工。該方法適用于大螺距的梯形螺紋加工,能夠有效提高車削質量與效率,避免產生扎刀問題,并且可采用宏程序進行編程處理,在梯形螺紋任意結構參數發生變化的條件下仍可保障螺紋加工精度。
2、 數控車床變速車削梯形螺紋的加工流程優化設計
2.1 常規加工方法存在的缺陷。
通過針對四類梯形螺紋車削加工方法進行綜合分析,提煉出保障螺紋質量的最優方法的基礎上,還應基于生產效率與加工精度層面進行工藝流程的創新。
通常利用數控車床以高轉速車削梯形螺紋時,往往面臨螺紋表面粗糙度不達標的問題,同時多個刀刃將產生較大的切削力與振動效應,易縮短切槽刀的使用壽命;在以低轉速車削梯形螺紋時,往往導致生產效率大幅下降,并且當速度驟然變化時易引發螺紋亂牙問題[2]。基于此,本文擬采用變速車削這一新型加工模式,首先利用粗車刀以高轉速進行工件外形的車削,保障工件的大徑、中徑和小徑數值均符合標準值要求;隨后再改用精車刀以低轉速進行工件的精車、修光處理,確保牙型角、牙頂寬與牙槽底寬等指標均符合要求。在此過程中,需注意控制好高轉速、低轉速與粗車、精車間的銜接過渡,保障梯形螺紋的加工質量。
2.2 變速車削加工方法的應用。
2.2.1 加工方案分析。
基于GSK980TD 數控車床進行梯形螺紋 Tr36×6 的變速車削加工方案設計,考慮到該梯形螺紋的螺距為 6mm、保持中等水平,因此可選用斜進法與左右切削法配合加工,基于 G76 指令進行切削加工,依次完成粗車、精車環節的編程設計,注意留足余量。
2.2.2變速車削加工程序設計。
在粗車前,首先以 X 方向為基準留出精車余量 X0.5,將車床轉速設為每分鐘 560r 的高轉速水平,待完成粗車后倘若直接將轉速調低進行精車,極易產生牙槽亂牙問題,并且易引發撞刀、刀片折斷等問題,因此需重點做好粗車后的速度調節與工序控制。粗車程序設計如下:
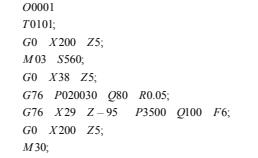
在粗車完成后,首先將粗車刀停放的位置設為 X200 Z5,隨后進入對刀界面在磨耗欄中輸入 U8 刀補,使坐標系上的原點朝 X 軸右側移動 4mm 的距離,此時刀尖較先前提高約一個 h3的距離;隨即將數控車床的轉速降低至每分鐘 25r,再次運行粗車程序,在此環節精車刀將位于靠近梯形螺紋表面的平面移動,確保不會接觸到梯形螺紋表面。此時觀察梯形螺紋車刀可發現,車刀所處位置較牙槽存在一定的偏移,應通過調試使車刀重新回到牙槽內,在此可將粗車程序中的起始點 Z0 調整為- 1,再次運行粗車程序,并同時校對車刀與梯形螺紋槽間的偏差值,調整至二者保持完全對正為止。接下來需針對偏移后的坐標系進行調整,在對刀界面磨耗欄內輸入 U- 8 并執行程序,即可使坐標系重新恢復至粗車加工模式下的坐標系,隨后再次運行粗車程序,倘若發現精車刀在車削加工過程中觸碰到牙槽,則需重新進行梯形螺紋的粗車加工,直至精車刀與牙型保持一致、無表面接觸為止。最后需針對梯形螺紋的小徑尺寸進行調節,選用左右切削法進行切削調試,確保精車螺紋兩側面的偏移量符合標準件設計要求;通過進入對刀界面調整磨耗欄中的 U 值,即可實現對中徑、小徑等尺寸的精確調整,并配合三針測量法進行測量,計算得出梯形螺紋左右兩側面的偏移值均為 0.26mm,確保最終加工出的梯形螺紋工件尺寸與精度達標。
2.2.3 調試結果。
通過針對變速車削加工的程序與具體參數進行多次驗證,最終確定標準化加工方案,即先以每分鐘 560r 的高轉速運行粗車程序、完成粗車加工,再將轉速調整至每分鐘 25r的低轉速水平,將定位坐標調整為 G0 X38 Z- 1.8,運行精車程序、利用精車刀進行工件左右兩側面的精修處理,最后針對中徑、牙頂寬、牙槽底寬等指標進行測量,以此判斷加工精度是否符合質量要求,提升梯形螺紋加工效率[3]。精車程序設計如下:
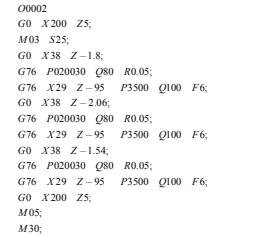
2.3 工藝優化的注意事項。
在采用數控車床變速車削工藝時,還應注意以下問題:首先是在切削過程中需補充足量切削液,在刀頭處增設頂尖,用于防止切削刀具在車削工件環節產生大幅振動,保障梯形螺紋副表面具備良好的粗糙度,并且在數控車床執行車削作業過程中做好操作人員的安全教育工作,禁止采用棉紗擦拭工件表面,避免引發安全事故或設備損壞問題。其次應注意在精車前做好中心孔的修正工作,針對螺紋同軸精度進行嚴格校正,并且做好精車刀質量的檢查,確保兩側刃磨平直且鋒利,保障后續加工環節的精車質量。再次是在車削加工梯形螺紋的過程中,應盡量調低切削用量,防止在后續切削環節因疏于管控造成工件變形問題;在裝夾工件環節,應注意控制好尾座套筒的伸長量,避免因套筒過短導致車刀退刀環節尾座碰撞床鞍。最后還應加強對梯形螺紋技術參數的把控,例如檢查梯形螺紋的中徑是否與基準軸位于相同軸線上,
中徑尺寸公差是否符合設計標準,大徑尺寸是否控制在標準尺寸以內,梯形螺紋牙型角是否為 30°,梯形螺紋左右兩側的表面粗糙度數值是否達標等。在利用數控機床加工梯形螺紋時,還應注意做好機床設備剛度、工件與刀具材料等指標的調節,并針對編程進行精細化設計,實現工藝優化目標。
3、結論
當前在采用數控車床進行梯形螺紋加工環節,常面臨粗加工吃刀深、切削余量大、生產效率低、表面粗糙度大以及編程復雜程度高等問題。對此需針對一般加工方法做出改進,引入變速車削工藝進行加工方法的優化,做好粗車與精車加工銜接環節轉速的調節、實現平穩過渡,避免刀具觸碰工件表面影響到加工質量,并完善程序設計與調試工作,保障提升梯形螺紋加工精度與效率,實現零部件批量化生產目標。
投稿箱:
如果您有機床行業、企業相關新聞稿件發表,或進行資訊合作,歡迎聯系本網編輯部, 郵箱:skjcsc@vip.sina.com
如果您有機床行業、企業相關新聞稿件發表,或進行資訊合作,歡迎聯系本網編輯部, 郵箱:skjcsc@vip.sina.com