葉輪加工中心床身動態(tài)特性分析與優(yōu)化
2018-1-18 來源: 北京信息科技大學 機電工程學院 作者:王 能,鐘建琳
摘要: 葉輪是航空發(fā)動機的重要組成部分,需要具有高的加工精度和質量。以某工廠生產的航空發(fā)動機葉輪專用加工中心床身為研究對象,采用有限元方法分析其動態(tài)特性。根據床身的固有頻率和模態(tài)振型找出其薄弱環(huán)節(jié),針對床身的薄弱環(huán)節(jié)提出相對的優(yōu)化改進意見,以改善床身的動態(tài)特性,并通過模態(tài)試驗驗證優(yōu)化的合理性和可行性,為以后的設計提供了一定的參考。
關鍵詞: 固有頻率; 加工中心; 動態(tài)性能; 模態(tài)試驗
0 、引言
隨著科學技術的發(fā)展,航空制造業(yè)的先進性成為了影響國家國際地位的重要標志之一。
針對航空發(fā)動機葉輪的特點,某單位自主研發(fā)了航空發(fā)動機葉輪專用生產設備。根據葉輪的加工工藝特點,要求機床具有高加速度、高精度、高剛度、大扭矩的五軸五聯動的特性。
提高制造設備的性能,保證葉輪的加工質量的主要手段之一就是機床的動態(tài)特性研究[1-3]。
目前,國內、外對葉輪制造進行了大量的研究,主要包括以下三個方面:
①運用計算機輔助手段對葉輪進行多學科優(yōu)化設計;
②優(yōu)化葉輪生產過程中的加工工藝,選取適當的加工參數和方法;
③提高葉輪制造設備的性能,保證其加工質量。
其中,提高制造裝備研究的主要手段之一就是機床動態(tài)特性研究。
本文即從改善制造裝備入手,通過應用 ANSYS Workbench 軟件對某工廠自主研發(fā)的航空發(fā)動機葉輪專用生產設備的主要結構進行分析和優(yōu)化來提高機床的動態(tài)特性,改善
葉輪的加工質量。
最后通過模態(tài)試驗驗證合理的優(yōu)化設計,不但提高了本臺機床的性能,為今后機床結構的設計尤其是主要受力部位設計也提供了一定的參考。床身是高速、高精五軸聯動銑削加工中心的關鍵部件,其動態(tài)性能直接影響到整個加工中心的加工精度、抗振性和穩(wěn)定性,同時,機床的床身承載了機床的所有運動部件,也是決定機床剛度的重要環(huán)節(jié)。
因此運用計算機輔助軟件對床身結構進行分析,觀察床身結構在各階模態(tài)下的振型和固有頻率,找出其薄弱環(huán)節(jié)并進行合理的優(yōu)化對改善機床整體的動態(tài)性能具有很大的意義[4-5]。
1 、床身結構特點
葉輪是由多個薄且為自由曲面的葉片構成,其技術要求為: 葉片型面輪廓度為 0. 1,直徑范圍 200 ~500,葉片前后緣尺寸最小為 R0. 1 ~ R0. 15mm,粗糙
度 Ra0. 8。采用鈦合金 TC4、高溫鎳基合金 GH4169 材料,如圖 1 所示。
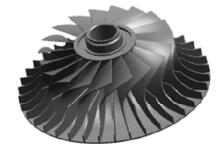
圖 1 葉輪
葉輪加工中心由床身、Y 軸滑座、X 軸滑座、主軸箱、擺轉臺等關鍵部件組成,其模型如圖 2 所示。與床身直接接觸的結構為 X 軸滑座和擺轉臺左、右兩箱體。其中,X 軸滑座通過滑塊-導軌結構與床身接觸;擺轉臺的左、右兩箱體則通過螺栓直接固定在床身上。
床身的材料是 QT500,查閱文獻[6]可知,該材料泊松比為 0. 275,彈性模量為 169GPa,密度為 7100kg /m3。
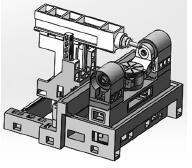
圖 2 葉輪加工中心模型
2 、床身有限元分析
2. 1 床身優(yōu)化前模態(tài)分析
利用三維建模軟件去除對分析無影響的倒角、小孔( 包括地腳螺栓安裝孔、導軌安裝孔等) ,以減少計算量,縮短計算時間。由于實際試驗狀況下,床身是 6個橡膠墊塊著地,故在橡膠墊塊的底面添加固定約束,圖 3 中的藍色區(qū)域為橡膠墊塊與地面接觸位置,查閱文獻[6]可知,橡膠墊塊材料的泊松比為 0. 49,彈性模量為 6. 1MPa,密度為
1000kg /m3。
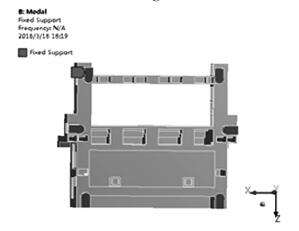
圖 3 床身施加約束
提取床身的前 3 階模態(tài),其固有頻率如表 1 所示,振型如圖 4 所示。
表 1 床身優(yōu)化前模態(tài)分析結果
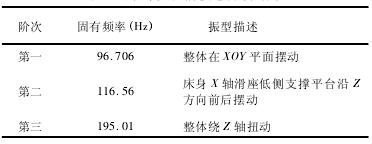
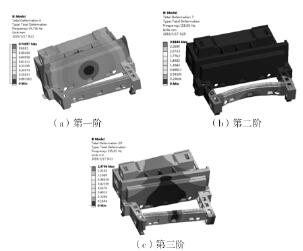
圖 4 床身前 3 階振型圖
從前 3 階振型圖可以看出,床身的 X 軸滑座低側支撐平臺的剛度較弱,最大的振幅發(fā)生在第二階模態(tài),達到了 2. 6644mm,由于床身的最大變形處支撐 X 軸滑座,因此床身的振動會直接傳遞到 X 軸滑座上,進一步傳遞到 Y 軸滑座與主軸箱上,從而引起刀具的振動,直接影響工件的加工精度和表面質量。
因此,對床身進行結構優(yōu)化改進,提高床身的剛度,改善床身的動態(tài)特性,進而提高整機的加工精度和抗振性。
2. 2 床身優(yōu)化后模態(tài)分析
結合床身的仿真結果和整機裝配關系可知,床身變形主要集中在 X 軸滑座作用位置。考慮到床身質量對動態(tài)特性的影響,在床身與 X 軸滑座接觸位置設計成回型筋板結的同時,通過填充兩側支撐板來提高床身剛度,以及平衡床身質量,優(yōu)化結果如圖 5 所示。
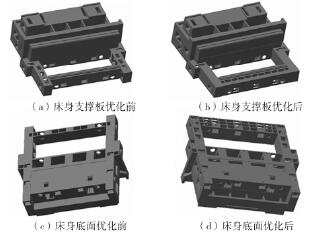
圖 5 模型優(yōu)化前后對比
對優(yōu)化后的床身結構進行模態(tài)分析,其處理方式與優(yōu)化前保持完全一致,提取床身的前 3 階模態(tài),其固頻率如表 2 所示,振型如圖 6 所示。
表 2 床身優(yōu)化后模態(tài)分析結果
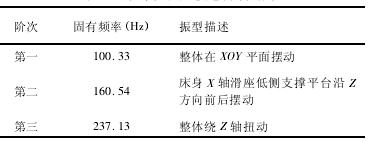
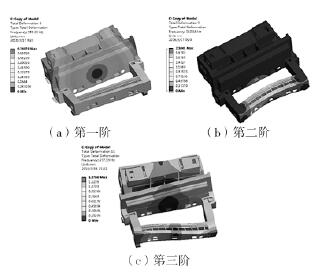
圖 6 床身前 3 階振型圖
由頻率和振型圖可知,優(yōu)化后的床身模型最大變形仍出現在 X 軸滑座低側支撐平臺處,但各階最大變形量與優(yōu)化之前相比之下均減少了,其優(yōu)化前后的結果對比如表
3 所示。
表 3 床身優(yōu)化前、后的結果對比
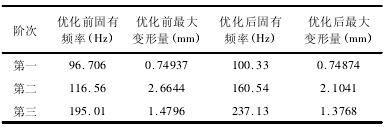
由表 3 可知,床身前 3 階固有頻率均有明顯提高,近似頻率下相對變形量有所減小,對于提高機床整機的加工精度至關重要,因此,針對床身的優(yōu)化是合理的。
3 、試驗模態(tài)分析
3. 1 試驗模態(tài)測試系統(tǒng)
工廠對優(yōu)化后的床身結構進行了生產,我們對生產后的床身進行模態(tài)試驗,本實驗采用 SIMO 錘擊法測試方式,試驗測量系統(tǒng)共由三個部分組成: 激振系統(tǒng),響應采集系統(tǒng),模態(tài)分析和處理系統(tǒng),圖 7 所示為測試系統(tǒng)原理簡圖。
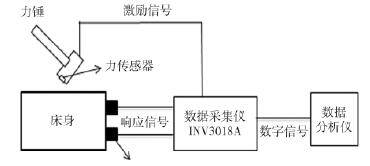
圖 7 測試系統(tǒng)原理簡圖
3. 2 試驗方案設計
3. 2. 1 支承方式
為盡量使床身的各階模態(tài)更好地顯示出來,在床身底面加上 6 個橡膠墊塊用來支撐床身部件。
3. 2. 2 激勵點和響應測點的布置
一般來說激勵點的布置原則是根據結構的特點和試驗目的,以不遺漏模態(tài)為前提而又盡可能簡化,此外激勵點還應避免在各階模態(tài)的節(jié)點位置,節(jié)點位置可由試驗前的有限元分析獲得。
響應測點位置以能反映零件的動態(tài)特性、振動明顯、能得到較好信噪比信號為原則[7],試驗響應測點布置如圖 8 所示。
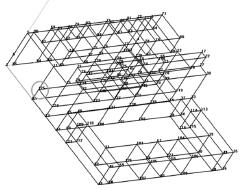
圖 8 激勵點和響應測點的布置
3. 3 模態(tài)試驗分析結果
采用東方振動噪聲研究所模態(tài)試驗測試分析設備Coinv DASP V10 中集總平均法進行模態(tài)定階識別,試驗后的床身模態(tài)頻率如表 4 所示,振型如圖 9 所示。
表 4 試驗模態(tài)分析結果
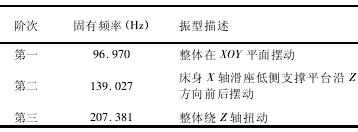
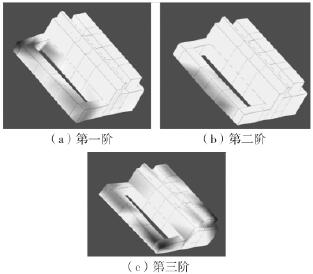
圖 9 試驗模態(tài)振型圖
3. 4 理論與試驗對比
通過試驗分析得到床身的前 3 階固有頻率并與其優(yōu)化后的理論分析結果進行對比,如表 5 所示,各階振型相同,同階固有頻率最大誤差為 13. 4% ,說明試驗結果與理論分析結果相一致。
表 5 理論與試驗分析結果對比
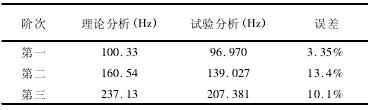
4 、結束語
本文以某工廠研制的葉輪專用加工中心為例,通過理論分析找出該加工中心床身結構的薄弱環(huán)節(jié),有針對性地提出優(yōu)化改進意見。
通過對比,優(yōu)化后的床身結構固有頻率有明顯提高,近似頻率下相對變形量有所減小。最后通過試驗驗證了該方案的合理性和可行性。本文所得的結論為改善整機的動態(tài)特性奠定了一定的基礎。
投稿箱:
如果您有機床行業(yè)、企業(yè)相關新聞稿件發(fā)表,或進行資訊合作,歡迎聯系本網編輯部, 郵箱:skjcsc@vip.sina.com
如果您有機床行業(yè)、企業(yè)相關新聞稿件發(fā)表,或進行資訊合作,歡迎聯系本網編輯部, 郵箱:skjcsc@vip.sina.com
更多相關信息