1 前言
D600B由東方汽輪機廠引進國外某公司600MW大型火力發電機組,它是實現600MW大型發電設備國產化的一個重要步驟,而噴嘴室的國產化是該機組實現國產化的重要內容之一。噴嘴室是高溫高壓蒸汽進入熱力循環的重要通道,在制造過程中保證設計的要求是保證機組熱循環效率的一個重要條件。
東汽廠首先采用了此結構設計,在設計的300MW機組中借鑒了國外某公司亞臨界600MW機組噴嘴室的結構,它主要由噴嘴室、噴嘴加強環、噴嘴葉柵三部分組成。但是D600B機組噴嘴室的結構與東汽300MW機組噴嘴室相比較,在噴嘴加強環的結構上有了很大的改變,它采用的是國外某公司超臨界機組和超超臨界機組噴嘴加強環的結構,其結構的改變大大地增加了加工的難度。
2 D600B噴嘴室及噴嘴加強環的結構特點
D600B噴嘴室的結構簡圖如圖1所示,主要由三部分組成:噴嘴室、噴嘴加強環及噴嘴葉柵,三部分通過焊接方式連接為一個整體。
噴嘴加強環是連接噴嘴室和噴嘴葉柵的過渡結構,圖2是根據設計要求通過PRO/E三維造型建模生成的噴嘴加強環三維立體圖。由于噴嘴加強環是高溫高壓蒸汽進入熱循環的重要通道,耐高溫高壓和可靠的連接強度就成為設計的必要條件,因此采用了高溫合金鋼材2Crl2NiMolW1V作為加強環本體的材料,毛坯為鍛造毛坯。在噴嘴加強環180度半環上設計了81個窄汽道和兩端各&個復雜結構的型腔。這種結構設計一方面可以最大限度地減少汽流在流動過程中的能量損失,另一方面也大大地增加了加工的難度。
3 噴嘴加強環結構工藝性分析
該結構在具備良好的設計性能的同時,犧牲了其良好的機械加工工藝性,給機械加工工藝方案的設計和如何實現其經濟高效加工留下了一個很大的難題,主要體現在以下幾個方面:
(1)零件材料選用2Crl2NiMolW1V,高溫合金鋼,鍛件毛坯。這種材料具有很高的機械強度,加工性能較差,加工時斷屑為帶狀,并容易出現燒刀、粘刀現象,給車削加工和銑削加工的刀具材料和切削參數選擇帶來很大困難。
(2)零件汽道型腔的尺寸小,加工深度大,銑削加工刀具的加工長度直徑之比較大,刀具的切削狀態很不理想,給銑削加工的切削參數選擇造成較大困難。
(3)汽道型腔形狀很不規則,結構復雜,其數控加工利用手工編程的方法無法完成加工程序的設計,必須借助于具有三維立體造型和加工程序自動生成及程序后值處理功能的程序設計軟件才能完成其數控加工程序設計。
4 噴嘴加強環機械加工工藝方案設計
4.1工藝方案的選擇
通過對噴嘴加強環結構特點及機加工工藝性分析,并結合東汽在$00+-機組噴嘴室加工取得的成功經驗,發現12003噴嘴室機械加工的難點主要集中在噴嘴加強環的加工,而噴嘴加強環的加工難度主要集中在噴嘴汽道型腔的加工上。由于其前所未有的加工難度,在其總體加工方案的制定上必須采取科學的態度,為此東汽廠進行了大量的前期方案論證工作。可供選擇的主要方案有:
(1)全部采用機械加工的方式;
(2)汽道型腔采用電火花加工,其余部位采用機械加工;
(3)加強環整體外購。
4.2總體加工方案的制定
在對噴嘴加強環多種制造方案的比較,并進行嚴格論證的基礎上,制定了如下的總體加工方案:以數控加工為主,輔以其它普通加工方式進行噴嘴加強環工藝設計。加強環出汽側的焊接坡口及進汽側焊接坡口除環狀型線外的其它結構尺寸用C516立車加工,進汽側環狀焊接坡口的型線和通流部位的型腔全部在數控滑枕床身數控銑床(XK7710A)上進行。
5噴嘴加強環數控加工刀具設計及關鍵工藝試驗的實施
5.1數控加工刀具的設計
數控加工刀具的選擇和設計是噴嘴加強環數控加工工藝設計的一個重要環節,全周81個狹窄汽道的結構尺寸較小,加工深度深,加工時刀具切削接觸面積大,刀具的切削加工條件較為惡劣。
經過本項目工藝試驗第一階段成果的總結,對噴嘴加強環的設計提出了改進意見,并對數控加工刀具進行了設計。對刀具材料選用了韌性及抗粘刀效果較好的鋁高速鋼,考慮到粗加工和精加工分開進行;在刀具結構上,設計了刀尖帶R1的立銑刀和球頭銑刀兩種結構,粗加工采用帶R1的立銑刀,精加工采用球頭銑刀,圖3所示是立銑刀和球頭銑刀的結構簡圖。
5.2噴嘴加強環汽道加工工藝試驗的實施
通過對噴嘴加強環結構工藝性的分析及在數控加工刀具的選擇和設計上所遇到的巨大困難,發現噴嘴加強環汽道型腔的數控加工方案是否可行,如何在程序設計過程中通過建立準確的數學模型體現設計特點,以及如何實現噴嘴加強環的高效、經濟加工是本項目能否取得成功的關鍵,所有這些都需要通過嚴格的科學試驗來驗證,東汽廠通過實施以下的工藝試驗對工藝方案的可行性進行了驗證。
5.2.1試驗目的
(1)驗證噴嘴加強環噴嘴數控加工工藝的可行性;
(2)驗證噴嘴加強環數學模型建立、加工程序自動生成、程序后值處理與設計要求的一致性;
(3)選擇合理的切削參數,提高加工效率,力爭實現噴嘴加強環的高效經濟加工;
(4)確定刀具的結構尺寸。
5.2.2試驗結果
兩個階段的試驗,進行了設計結構的工藝性改進,加工程序的精確設計,加工刀具結構設計的改進,驗證了600MW噴嘴加強環汽道數控加工工藝方案設計、數控加工程序的設計是切實可行的,并且通過試驗總結出了實現其經濟、高效加工的刀具材料和合理的切削參數,達到了試驗的目的,解決了600MW噴嘴加強環汽道加工的難題。
6 D600B噴嘴加強環數控加工程序設計
D600B噴嘴加強環結構復雜,汽道部分是由多張曲面組成,手工編制該零件的數控加工程序根本無法進行,只有采用自動編程系統編制程序。使用自動編程系統編制數控加工程序,首先必須準確地建立被加工零件的三維實體圖,有了三維實體圖才能進行模擬加工、干涉檢查以及數控加工程序的生成。
6.1模型的建立
由于D600B噴嘴加強環結構復雜,模型的建立困難,特別是加強環兩端的汽道更復雜,設計圖紙只給出了三個截面的型線,見圖4。
圖紙給出的信息不足,按照圖紙給定的信息,在01234軟件中無法建立零件的模型,如何利用01234軟件中基本功能建立出光滑過渡的汽道,又能滿足設計的要求是噴嘴加強環數控加工的又一個難點。
針對上述問題,主要采取以下技術措施:分析加強環的結構,根據設計圖紙給出的信息,由于汽道的進出汽側的結構截然不同,見圖5,結合PRO/E軟件中具有的建模功能。在建模中,將汽道分為兩部分,分別用不同的建模方式建立,進汽側采用變截面旋轉方式建模,出汽側采用變截面拉伸方式建模,兩曲面的過渡采用變5的倒角方式。通過采取上述措施,完成了模型的建立,所建立的模型完全達到了設計圖紙的要求,而且整個汽道是光滑過渡的。
6.2NC加工
PRO/E加工模塊提供了常規的加工方法,其加工方式缺乏很大的自由度,01234生成67程序存在的主要技術難點如下:
(1)自動生成的程序繁瑣,加工效率低。如在精加工汽道時,采用窗口加工方式自動生成的刀具軌跡見圖6,由于已經過了粗加工,被加工曲面的余量只有1mm,自動生成的刀具軌跡有空走刀現象。
(2)自動生成程序的走刀軌跡與實際加工要求差距較大。在加工噴嘴加強環外側兩端!,9坡口時,由于加工余量大,而且不均勻,實際加工中是采用Ф100的盤銑刀加工,走刀軌跡要求分層切削,這樣加工效率高,用PRO/E自動生成的程序無法達到上述要求,生成的加工軌跡見圖7。
(3)加工區域過小,造成刀具在切入時有扎刀現象。在加工不封閉曲面時,在01234軟件中刀具的軌跡是沿著被加工曲面的邊界切入的,而實際加工時,由于該零件其它部位還有加工余量,因此被加工曲面大于零件的曲面,造成扎刀現象。
針對上述技術難點采取的主要技術措施:
(1)在完成零件的粗加工后,在零件毛坯上將粗加工的余量去除,精加工時毛坯只留有1mm精加工余量,以減少空走刀現象。
(2)利用PRO/E軟件中的體積加工的功能,將希望的走刀軌跡的范圍作為輪廓建立被加工的區域,達到分層切削的目的。
(3)加工外側兩端45度坡口時,將被加工曲面延伸,加大加工區域。
6.3后置處理程序的設計
自動編程系統的生成加工程序的過程是經過刀位計算產生刀位文件(CLDataFile),而不是直接用于加工的數控加工程序。因此,需要把刀位文件轉換成指定數控機床能執行的數控加工程序,才能進行零件的數控加工,把刀位文件轉換成指定數控機床能執行的數控加工程序為后置處理,由于各種機床使用的數控系統不同,所用的數控加工指令代碼及格式也有所不同。PRO/E軟件配置了通用后置處理器,針對ZK7710A數控銑床,編制了該機床的專用后置處理程序。PRO/E軟件后置處理器見圖8。
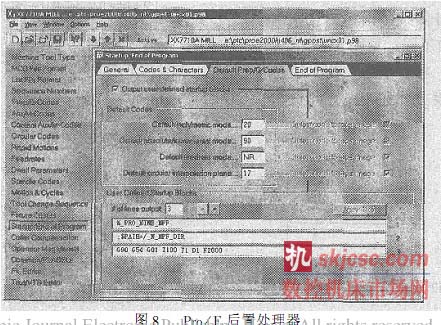
經后置處理產生的程序格式如下:
主程序格式:
7 加工驗證
D600B噴嘴加強環的首件試加工,在數控機床上的加工程序全部由PRO/E軟件自動生成,直接用于加工。由于所有加工程序都在PRO/E.軟件中進行了干涉計算,提高了加工程序的準確性及可靠性。經檢查,加工的產品完全符合設計圖紙的加工技術要求。
8 技術經濟效果
通過對PRO/E軟件的開發,(1)成功地完成了噴嘴加強環的建模、NC加工、后置處理以及加工程序的生成。由于加工程序在系統中通過了過切檢查計算,因而保證了加工程序的正確性及可靠性,減少了程序在機床上的調試時間。(2)確定了噴嘴加強環數控加工方案的可行性。通過工藝試驗,獲得了合理的切削參數,根據試驗結果對加工工藝及刀具的改進,大大地提高了噴嘴加強環數控加工的效率達1倍以上。
在數控機床上加工的噴嘴加強環汽道型面光滑,修磨量小,大大地減少了鉗工的工作量,且加工效率高、質量好。每生產一副該噴嘴加強環可為工廠節約57.8萬元,因此,該項目的經濟效益和社會效益是巨大的。
9 結論
D600B噴嘴加強環在XK7710A數控銑床上加工方案是成功的,已應用于D600B-041120A噴嘴加強環的加工工藝中,加工出的產品完全達到了設計圖紙的要求,解決了600MW噴嘴加強環在機械加工上的難題,實現了600MW機組噴嘴室的全部國產化制造,為實現600MW機組汽輪機國產化做出了貢獻,為東汽進行600MW超臨界、超超臨界機組的開發奠定了基礎。
如果您有機床行業、企業相關新聞稿件發表,或進行資訊合作,歡迎聯系本網編輯部, 郵箱:skjcsc@vip.sina.com